Introduction: Hardwood Kubb
Kubb is a yard game that's quickly rising to the popularity of Cornhole (or sack toss, or whatever your region calls it).
Kubb is played on an open field, or pitch, and teams take turns tossing batons at Kubbs in an attempt to knock them down. It's a little more complicated than that, but not much. Kubb fits in a five gallon bucket, and can be played on any flat surface that's big enough - back yard, parking lot, beach, etc.
This Instructable is all about how I (over)built a Kubb set from hardwoods.
Resources:
For basic Kubb info, check out the Wikipedia.
For details on Kubb dimensions, a rules video, and details on the 2020 Championship, check out USAKubb.org.
Disclaimer:
You'll notice my shop is filthy. It's in a barn. My tools are mostly garage sale and craigslist finds. I don't believe you need a $3000 table saw to make cool stuff.
Step 1: Materials
My first Kubb set was built from 4x4s scavenged from an old pallet and some curtain rod from a hardware store. It worked well, but the dimensions weren't quite right. Basically, I had slapped it together just in time for a shindig at our house. I didn't want to spend much time or money on it, because I didn't know if anyone would even play. But it must have been a success, because by the end of the night people were still in my yard playing with headlights on.
Most people use fir or pine to build a Kubb set, which works really well. It's inexpensive and easy to work with. I haven't seen anything saying what type of wood you're supposed to use, but there are some size and weight recommendations to follow. But, if you followed the resources link in the previous step, you'll notice the not-so-official "official" rules and pitch size seem to vary a bit.
Anyway... My pallet wood set started falling apart from all of the use it was seeing. In defense of my craftsmanship, part of it also had to do with having a Golden Retriever that brings the batons back with fresh chew marks. So, without telling my wife how much money I was going to spend (read: waste) to build a lawn game, I headed off to the local Edensaw Woods. Edensaw is a mill and importer of ethically sourced hardwoods, and their less expensive B grade lot is where I usually end up.
For this project, I would need:
~6 board feet of 1x4 for the kubbs (Red Oak)
~2 board feet of 2x4 for the batons (Walnut)
~2 board feet of 1x4 for the king (Mahagony)
Exterior grade Wood Glue
Eurethane (Arm-R-Seal)
Step 2: Cutting It Down
This is the first actual build step.
Wood is selected, plans are gathered... or rather a set of dimensions have been hastily converted from the metric ones I could find on the internet.
Kubbs:
Quantity 10 @ 2.75" x 2.75" x 6" each
This means I need one piece of wood glued up to about 3" x 3" x 72"
The oversize dimensions give me some room to cut a rough-glued piece down to a perfect shape, plus room for sawblade kerf and a spare kubb to practice finishes or corner-rounding on.
Batons:
Quantity 6 @ 1.75" round x 11ish" long
I bought one 2" thick piece of walnut with the intention of turning it down to the 1.75" finished diameter. So I would need to cut it into 2" strips. Since the walnut is from the B-grade material, it was warped and rough. When this is the case, ripping a long piece isn't ideal. Instead, it was better to minimize the warpage by cutting the block to 12" long pieces, then ripping into 2" strips.
King:
Quantity 1 @ 3.25" x 3.25" x 10"
I had this piece of Mahogany laying around from an old project. My barn isn't exactly climate controlled, so it had a bit of a curl to it. But it wasn't so bad that glue and big clamps couldn't square it up.
Step 3: Gluing It Up
There are a few things your shop teacher may have taught you about gluing: grain direction, glue quantity, clamping force and clamp spacing.
I've heard to alternate grain, and I've heard to stack the grain. But my wood is a little warped, so I'm going to alternately stack the grain so minimize having to put too much clamp pressure on it.
I'm a big fan of this glue brush from Rockler. It lasts basically forever, and instead of cleaning wet glue from it, I can just wait till it dries and it peal the glue out of the silicone bristles.
It's important that a glued joint has adequate coverage so there aren't any dry areas. Too much glue, and it's a mess. I glue up on a piece of plastic, which makes cleanup pretty easy.
Clamps should alternate directions when possible. Sometimes I'll add a strip of sacrificial wood between my glued pieces and the clamp. This can do two things: 1. it won't leave clamp marks; 2. on thinner glue-ups, it will distribute the force of the clamp over a wider area, so you get more uniform clamping.
The mahogany I'm using for the king was pretty warped, so I had cut it into smaller pieces to minimize the effect of the warp.
Step 4: Cutting It Down... Again
Kubb:
I've got one six foot long by 3"x3" chunk of red oak. I cut this down to as many 6" long Kubbs, then trimmed 1/8" off all sides. Next thing you know, I've got 11 Kubb pieces at 2.75" x 2.75" x 6".
King:
The King is a bit bigger than the Kubbs, so it's a bit trickier to cut with a 10" table saw. You'll notice in the photos that my saw blade can't quite connect. I could adjust my King dimensions, run it through a band saw, or just flip it and cut it. This last one is where you really learn if your saw is dialed in or not. Mine left some uneven marks, but nothing that couldn't be cleaned up with a sander.
My radial arm saw doesn't cut material this thick either, so out comes the crosscut T-bar for the end cut.
I cut a couple extra kings for a later step.
Step 5: Chucking It Up and Turning It Down
The Batons are the funnest part of this build.
I ran into some issues when I pulled out my lathe: someone hid my chuck from me. All I had was the flat mount chuck, so I'd have to improvise...
Since the Batons are all the same size, turned down from the same 2x2 blanks, I slapped together a quick jig to chuck them into. It's just a square hole cut into a oak scrap, secured to the flat chuck. The only significant disadvantage would be the inability chuck a piece back into the lathe accurately. So each piece would have to go from rough cutting all the way to finish without removing it.
I also needed a way to measure the diameter of each baton. For this, I took a piece of scrap, drilled a 1.75" hole near the end and cleaned it up with the band saw. This made it pretty easy to turn it down until it was close, then sand until perfect.
You may notice that the batons don't have the same groove patterns. This was how I hid a mistake: one of the batons chipped out while cutting a groove, so I widened the grove enough to remove the chips. Then I made the next one match the wide-grooved one. And the last two got a different design so it wouldn't look like I messed up. I meant to do that...
Step 6: Trimming It Up
King Kubb
This guy is bigger and grander than the rest. It only gets thrown at once or twice a game, and it sits in the middle of the pitch.
I cut a couple practice kings out of scrap 4x4 so I could test my king design.
The cornices on the top are made by running it through the table saw with the blade at an angle. In theory, you could use the same technique to cut the groove in it, but it just so happened I have the perfect tool for that...
I got it at a garage sale for like 5-10 bucks. I thought it was a dado set, but turns out it was a shaper set. It pretty handily chucks into the table saw, as long as you have the right cover. Anyway, I digress...
Practice cuts looked good, and although I thought to myself, "Harder woods are more likely to chip out", I neglected to test this theory with scrap mahogany. Tisk tisk.
The first groove I cut into it took a huge chip out. Luckily, I've made plenty of mistakes before, so I knew how to handle this. First, masking tape on the surfaces would minimize any more chipping problems. This is an absolute necessity when cutting counter tops, melamine, or laminate floors. Next, the chips were actually so big that I was able to recover them and glue them back into place. Pro tip: for small chips, mix sawdust and glue and use it like a paste. It'll stain pretty well, and looks way better than color matching the little puddy jars you can get in the stain section.
Step 7: Polishing It Up
I'm going to be honest; I hate sanding. I went with 100 grit, 250 grit, good enough on this one. It doesn't need to be super smooth, because I'm using it outside and i'm going to ding it all up. Or that's how I'm justifying it.
Fathers day tip: pick up some bench cookies from Rockler for dad. No-slip, no-scratch, and you can get staining stands for them.
I do all my staining on a 1/2" chunk of polypropylene. It's scrap from work, it's inert, and it cleans up easily. Nothing sticks to it.
I chose Arm-R-Seal for this project, because it's easy to use, has a natural look, provides adequate protection, and I had a half-used can on my shelf.
Look at that grain pop!
Step 8: Knocking 'em Down
Time to play!
For a good rundown on rules, check out Master of Games. They sell sets, too.
You may notice that I didn't make any line markers. Instead, I use Turf Marking Paint, like Rustoleum Industrial AF1600 (But maybe don't use that at your public park).
The big question after spending a bunch of time and money on a hardwood Kubb set: How does this set compare to a lighter soft-wood kubb set?
The batons don't turn end-over-end as quickly.
The king is harder to knock over.
It makes a satisfying "bonk" sound when you hit a kubb.
Overall, it's a bit different, maybe harder, to play. But it feels heavy and quality when you're throwing.
This set I'll keep away from the Golden Retriever...
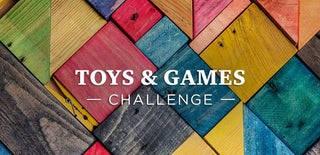
Second Prize in the
Toys and Games Challenge